Metal Stamping
Metal stamping, also called pressing, is a manufacturing
process used to convert flat metal sheets into specific shapes.
It is a complex process that can include a number of metal
forming techniques — blanking, punching, bending and piercing,
to name a few. Metal stamping is a fast and cost-effective
solution for large-quantity manufacturing need.
Custom Metal Stamping
Custom metal stamping describes metal forming processes that
require custom tooling and techniques to produce parts specified
by the customer. A wide range of industries and applications
employ custom stamping processes to meet high-volume production
needs and ensure all parts meet exact specifications.
Custom Tooling Manufacturing
When discussing the stamping process, invariably the discussion
will lead to the dies. It would not be an exaggeration if the
die were to be described as the 'life' of the stamping. The
precision of the die very much decides the quality of the
product in the end. The die consists of a top part and a bottom
part. The parts are combined together, a metal plate is inserted
in between the gap, and pressure is applied. A die consists of a
few hundred to a few thousand parts, thus making it an extremely
complex component. The manufacture of a die is a matter of
particular technical skill for us.
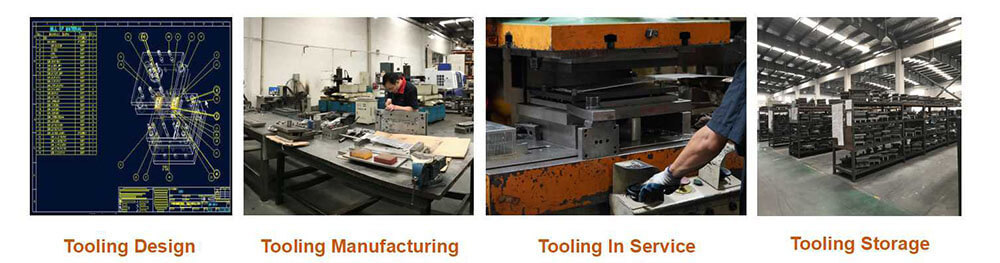
Tooling Material:
- 45#
- CR12
- CR12MOV
- SKD11
Tooling life:
- Cold plate, 10,000 shots--20,000 shots
- Normal, 200,000 shots--300,000 shots
Difficulty in Stamping
In the stamping, if the stamping machine is operated by setting the die and the material, we can manufacture the same product again and again with high precision. However, difficulties do arise in the steps before the machine begins smooth operation.
For example, the feed widths of the material when the machine is not warm and when it is warm may differ slightly. When continuous coining processing technology, where all the processes are sequential, is carried out, even a slight gap can turn into a bigger gap at the end, which may affect the quality severely.
The temperature and the humidity can also affect the process, as can the quantity of the machine oil used. It is not just about setting up and pressing the button. Without the fine tuning, a product with high precision will not be obtained.
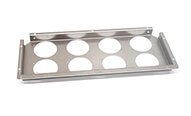
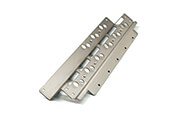
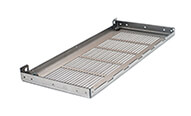
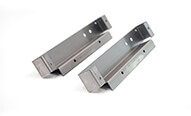